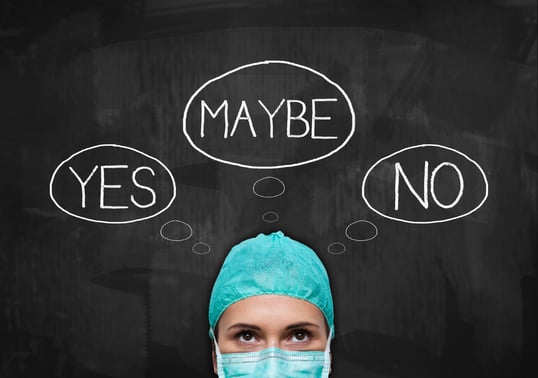
If you’ve read the post about distributed and centralized bypass architectures, you’re probably evaluating the right architecture for a new datacenter, or maybe you’re re-designing the one you’re currently using. The decision is not easy and it will often impact the operation and performance of the power protection system in your datacenter or the connected loads. Unfortunately, in technology there is rarely a simple “yes – no” or black – white” answer, and this holds true for power distribution as well. Yet, in technology and science, there’s a “grey area”, in which the ‘right’ decision is strongly influenced by the specific context and case, and is dependent on many parameters. Luckily, there are paths to find the best solution as a trade-off between the multiple parameters involved.
If you’re considering the use of an Uninterruptible Power Supply (UPS), it means you are worried about the possibility of utility power failures and the associated downtime problems that follow. Given this, the selection of the appropriate configuration or architecture for power distribution is one of the first topics of discussion, and the use of a centralized, parallel, distributed, redundant, hot-standby or other configurations available, becomes an important part of it. While there are numerous architectures to choose from, there are also several internal variables that will require your attention. Fortunately, a few elementary decisions will make the selection easier. Even if not all parameters can be matched, it’s important to at least begin the conversation and explore trade-offs and other considerations. Without trying to be exhaustive (which would require a dedicated white paper), you should consider at least the following:
a) Cost: more complex architectures will increase both your initial investment and your cost, not only at the initial design stage but during the entire life of your power system, especially with regards to efficiency. In other words, we could say that complex architectures will increase your TCO.
b) Availability and reliability: how reliable should your power system be? And what about single or multiple points of failure? Would you need any type of redundancy?
c) Plans for growth: Do you expect your power demand or capacity to increase in the future? Will you re-configure your load distribution?
d) Related to the previous point, but highlighted separately because of its importance for UPS is modularity. Do you need a modular solution for future expansion or redundancy?
e) Bypass architecture; an important point as explained in a separate post.
f) Need for monitoring of the complete UPS power system, also considering any shutdown of loads, and in combination with other systems like thermal management.
g) Service and maintenance: Once the initial investment in power protection has been made, please do not forget to keep it at optimum conditions. This maintenance at regular intervals has to be achieved through service contracts, check for spares availability if multiple types of UPS are used, capability to isolate a subset, or use of remote diagnostic and preventive monitoring services such as Emerson Network Power’s LIFE for maximum availability.
h) Profile of the loads; especially if you’re considering a few large loads or many “small” loads (perhaps distributed across several buildings or in a wide area such as a wind farm), autonomy required for each load, peak power demands, etc.
In addition, the decision is not only related to the internal requirements of the power systems, but it is also linked to the type of load or application to be protected, as requirements and decisions may vary depending on the application being industrial, education, government, banking, healthcare or data center. For example, an application where the loads are servers which manage printers in a bank, compared to a hospital where the power protection systems may manage several surgery rooms, are by no means the same. In fact, in the case of bank printers, in the worst case they can be shut down, while in the case of the surgery rooms, their shutdown is not an option unless for scheduled maintenance. This is because a non-scheduled shutdown of the medical equipment in a surgery room would have a serious impact on the people inside that room for a surgical operation.
Let’s take the hospital example further and consider a particular case. In order to do a quick exercise and simplify, we can use a scenario with several surgery rooms as a reference (for example 5 to 20 rooms, each one with a 5-10 kVA UPS for individual protection), plus a small data center (for example with 30 kVA power consumption) and finally, other critical installations in the facility (let’s assume 300 kVA for offices, laboratories, elevators, etc.).
In this scenario, initially, the architectures that could be envisaged as a first step are:
1. Fully distributed, and for simplicity’s sake, a hospital with 10 surgery rooms is assumed here with 10 kVA for each surgery room plus a centralized UPS (>330 kVA) for the remaining loads.
2. A fully redundant solution based on a centralized UPS protecting all the loads (this UPS being in a parallel redundant configuration). The power for any of these UPS would be 300 kVA + 30 kVA + (10 x 10 kVA).
3. An intermediate solution, referred to as “redundant hot standby”, so that this redundant UPS is sized only for the surgery rooms (10 surgery rooms x 10 kVA), and with a bypass line connected to the large centralized UPS (>430 kVA). This solution shows the advantage of a smaller capacity required for this redundant hot standby UPS.
Emerson Network Power has done several simulations based on typical scenarios as the one described above for a hospital, and considered the factors for optimization a), b), e) and h). Considering the parameters for optimization, the energy savings (power consumption and heat dissipation), initial investment (CAPEX) as well as the maintenance costs (OPEX), the solution based on the “redundant hot standby” seems to be the most convenient.
Moreover, the difference between architectures 1 and 3 is larger as far as quantity of surgery rooms or period for cost simulation (from 1 year up to 10 years).
This points us in the right direction in selecting the best distribution architecture for this application in hospitals and using these parameters for optimization. Clearly, it can be enriched using the other parameters shown in the sections above, or adapted to the particular case (quantity of surgery rooms, autonomy for each load, power demanded by CPD room, reliability, …) that could lead to a different choice, but globally, this redundant hot standby has resulted in a good trade-off.
As said at the beginning, there is no magic solution for the optimum selection, but we have sought to explore several guidelines and check points that will help drive you towards the best solution for your case. Of course, any additional variables and the reader’s experience are welcome and can only serve to enrich the discussion.