Industrial generators are an organization’s lifeline to keep business running in the most critical of situations. In the instance of Healthcare facilities, their lifeline variable extends all the way to saving lives. With this type of responsibility, you’d think an organization’s standby power solution or plan would be continuously top-of-mind, but this is not always the case. Unfortunately, the old saying “out of sight, out of mind” usually proves to be true.
In many instances, industrial generators aren’t thought about until they are actually needed. And the other 99.9% of the time, they’re just sitting “out back” collecting cobwebs or worse—critters. That is, until the next emergency situation when the power goes out and suddenly, the generator is expected to be the star of the show. No time for a dress rehearsal, it’s opening night, and the curtains are opening if you’re ready or not.
So, what happens in that emergency situation if the lights fail to come back on??? It happens more often than Facilities Managers would like to imagine. But why is this the case? Isn’t a generator supposed to save you and your facility in your time of need? Yes, but you have to meet it halfway. The number one reason a generator fails to generate power during these critical times? Lack of maintenance.
Like every other piece of your critical infrastructure, your standby power solutions need tender love and care. Just like your car before going on a long road-trip, you want to make sure your vehicle is in good working condition, with enough gas and oil to get you where you’re going. Otherwise, you run the risk of being left stranded on the side of the road. Or in the case of the generator, left in the dark of your building when it’s without power (and losing revenue… or worse).
Maintenance programs comes in many forms, and dictated by either the nature of your business (i.e. Healthcare having specific requirements defined by HIPAA and NFPA) or your organizationally defined plans. Some look at a once-a-year check-up as being sufficient, but that's just the bare-minimum. Okay, at least you’re acknowledging it’s existence, but we at DVL recommend a check-up at least once a year as the better you are with the maintenance, the less time you’ll have to spend there, and also, the life of your equipment will be extended. Above all, however, you will have piece of mind knowing that it hasn’t been anywhere close to 364 days since a trained factory technician took a look at your equipment. Therefore, quarterly or even monthly check-ups are recommended, which are preventative maintenance program that exist for the more critical of facilities.
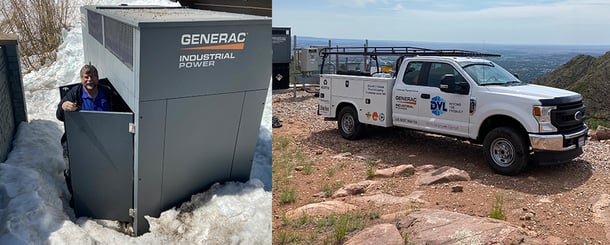
These visits include a variety of steps, beginning with Jobsite Safety Assessments. If you’re not intimately familiar with industrial generators, they can be dangerous. Our factory-trained DVL Technicians advise customers to do cursory checks around the GenSet areas, but to leave the more technical of steps to certified professionals. Our teams go beyond “run tests” by checking filters, fluid levels, and performing batter checks; along with manufacturer defined diagnostic tests.
In our recent #BeyondTheProduct podcast, we sat down with Generator Service experts to discuss the details and more. Give a listen, or check out information on DVL product and service options from Generac Industrial Power on our website.