Written By: David Klusas, Emerson Network Power
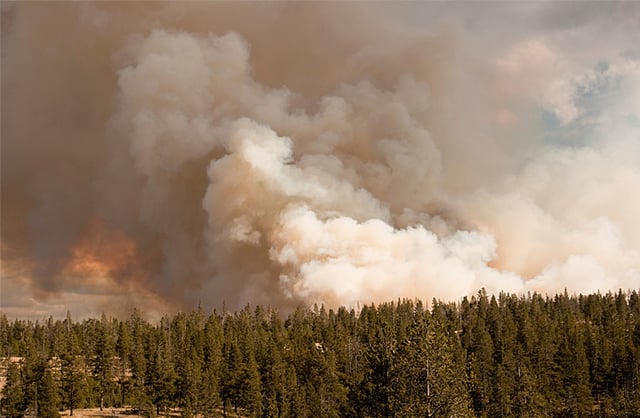
You can say what you want about mink farms, but one thing is certain: They stink!
That can be a problem if you’re operating a data center near one and trying to use airside economizers to bring in fresh outside air for free cooling.
There are many efficiency benefits to utilizing outside air for economization, but not every situation is right for bringing outside air into a data center. Each type of economizer has its own advantages and challenges, depending on data center goals, site requirements, geography and climate.
I recently visited four data centers, from Canada to Utah, including the one next to the mink farm, and found multiple occasions where airside economization was not the ideal solution, despite its energy savings.
One data center in Canada was near a heavily forested area, and the company was concerned about smoke from forest fires entering the facility. A data center in Washington was next to an apple orchard, which creates a lot of dust during harvest. Another is using 100% outside air for economization, but has an 8MW chiller plant for backup, in case they ever need to close the outside air dampers and recirculate the indoor air. That’s a HUGE initial investment for only a backup system.
Data centers have made cutting energy consumption a priority to save money and meet government regulations. Cooling accounts for almost 40 percent of data center energy usage, so it’s a main focal point for driving energy savings. More recently, water conservation has become a priority in the selection of cooling systems and economization strategies. At the same time, relative cost and the payback periods remain key factors in selecting these large, expensive systems.
All economizer systems use either outside air and/or water to reduce or eliminate mechanical cooling in data center cooling units. These economizer systems generate significant energy savings of up to 50 percent, compared to legacy systems. The first decision most data center managers make in selecting an economization strategy is the type of data center environment they want to operate, which naturally then leads to a decision on whether or not to bring outside air into the data center. As a result, there are two primary economizer designs typically deployed in data centers: direct and indirect.
While direct and indirect economizers operate in different ways, the ultimate goal of both systems is to provide free cooling to a room or facility, thus reducing the overall energy consumption of the facility. However, fundamental differences between the methods in which direct and indirect systems economize greatly impact the temperature and humidity environment that can be efficiently maintained within the data center.
Direct economization brings outside air into the data center using a system of ductwork, dampers, and sensors. These systems usually have lower capital costs than other forms of economization and work well in moderate climates. In the right climate, direct outside air economizers can be very efficient and an effective economization strategy, but do introduce the risk for contaminants and wide humidity swings into the data center. For maximum annual savings, a wide acceptable supply air temperature and humidity window needs to be implemented in the data center. For highly critical data centers, the risk of outdoor contaminants and wide temperature and humidity swings is sometimes too significant for comfort.
In contrast, indirect economizers can offer significant energy savings while limiting the prior concerns. Indirect economizers do not bring outside air into the data center, but instead use an indirect method to transfer heat from the data center to outside the building. There are primarily three types of indirect economizer technologies:
• Air-to-air heat exchangers, or heat wheels, in a wet or dry state
• Pumped refrigerant economizers, such as the Liebert® DSE™ system economizer
• Cooling towers for chilled water systems
Sensible air-to-air plate frame heat exchangers transfer heat between two air streams, but maintain a complete separation, thus eliminating the opportunity for contamination and transfer of humidity into the data center space. These units can be operated in a dry state, or can be sprayed with water to increase their effectiveness and hours of economization. Heat wheels offer similar qualities to air-to-air plate frame heat exchangers, but can have higher air leakage rates and require additional maintenance to maintain their performance.
The Liebert DSE system is a direct-expansion (DX) system that utilizes an integrated pumped refrigerant economizer to maximize annual energy savings and provide superior availability without the need for separate economization coils. When outdoor ambient temperatures are low enough, the integrated refrigerant pump is used to circulate the refrigerant in lieu of the compressor to maintain the desired supply air temperature. The refrigerant pump uses a faction of the energy used by the compressor. As the outdoor ambient temperatures rise, the Liebert DSE system automatically transitions on compressors to maintain the desired supply air temperature. Its integrated Liebert iCOM™ thermal controls work to automatically optimize the entire system to provide more free-cooling throughout the year.
Because of its efficiency advantages, the Liebert DSE system was recently approved for use in California data centers under Title 24. Its economizer was shown to reduce time dependent valuation (TDV) by 8-10 percent and, since it uses no water, save around 4 million gallons of water annually in a 1MW data center, compared to water economizers.
Initial installation costs for any of these economizer options can be affected by how well the technology under consideration fits into the overall design of the existing facility. The amount of indoor, outdoor or rooftop space required for situating the units will affect the selection decision. Chilled water systems with cooling towers tend to be the most costly, because of the high system first cost, use of water and a higher maintenance burden relating to their complexity.
Emerson Network Power offers options for all of these economizer technologies. There is no single economizer technology that fits every situation. Each has its own strengths based on location and application, and each has its challenges. Fortunately, there’s an economization option for virtually every location – even next to a mink farm.